Operating switches are vital components in control systems, providing direct control over machinery and processes in industrial and commercial applications. From starting and stopping equipment to selecting operating modes and ensuring safety, these switches are the primary interface between users and automated systems. This article provides a comprehensive guide to operating switches, including their types, uses, configurations, and maintenance tips, and explores their crucial role in automation and control systems.
What Are Operating Switches?
Operating switches are devices that control the flow of electrical current to machinery or processes. By physically activating or deactivating circuits, these switches allow operators to control functions like turning machines on or off, selecting modes, or activating emergency stops. Their design can range from simple toggles to complex, multi-position selectors, depending on their application within a system.
Types of Operating Switches and Their Functions
Toggle Switches
Toggle switches are commonly used for basic on/off control in many applications. With a lever that flips between two positions, these switches are widely used for simple power control.
- Features: Reliable, easy to operate, typically used for straightforward on/off functions.
- Applications: Lighting systems, power control, manual overrides in industrial machines.
Push Button Switches
Push button switches activate or deactivate circuits when pressed. They can be momentary, where they return to the original position after being pressed, or maintained, where they remain in the new position.
- Features: Available in a range of colors for easy identification; simple and versatile.
- Applications: Emergency stops, machine start or stop buttons, control panels.
Selector Switches
Selector switches allow users to choose between multiple modes or operating states, often using a rotary dial. These switches are essential in systems that need to alternate between different operating modes.
- Features: Multi-position control; often includes labeled positions for different modes.
- Applications: HVAC systems, production line controls, equipment with various operational settings.
Limit Switches
Limit switches detect the position of objects, activating or deactivating processes based on movement or placement. These are often used for safety interlocks and automated equipment.
- Features: Mechanical or electronic sensing; responds to physical contact or proximity.
- Applications: Conveyor systems, automated doors, safety interlocks, positioning controls.
Proximity Switches
Proximity switches detect objects without physical contact, typically using electromagnetic fields or light sensors to sense the presence of an object. These switches are ideal for automated systems that require non-contact detection.
- Features: Non-contact operation, minimizes wear and tear, suitable for high-speed detection.
- Applications: Assembly lines, packaging systems, robotics, material handling.
Emergency Stop (E-Stop) Switches
Emergency stop switches are critical safety components that allow immediate shutdown of equipment in emergencies. Typically large and brightly colored, E-stops are placed within easy reach of operators for quick access.
- Features: Engages immediately when pressed, stays locked until reset, often mushroom-shaped for visibility.
- Applications: Industrial machinery, assembly lines, hazardous equipment, automated systems.
Configurations and Installation of Operating Switches
Operating switches come in various configurations, each suited to specific applications and requirements.
Pole and Throw Configurations
Switches are classified by poles and throws, which determine how many circuits they control and the number of operational positions they have.
- Single Pole, Single Throw (SPST): Controls one circuit with one on/off position, commonly used in basic power control.
- Single Pole, Double Throw (SPDT): Allows switching between two positions, making it ideal for mode selection.
- Double Pole, Single Throw (DPST): Controls two circuits simultaneously, often used in high-power applications.
- Double Pole, Double Throw (DPDT): Controls two circuits with two positions, suitable for complex multi-mode functions.
Mounting Options
Switch mounting options depend on the environment and usage requirements:
- Panel Mounting: Installed on control panels for easy access; suitable for toggle, push button, and selector switches.
- Surface Mounting: Often used in industrial settings, where switches are exposed to dust and moisture.
- Flush Mounting: Provides a streamlined look, typically used in environments where aesthetics are important, such as labs or medical settings.
Applications of Operating Switches in Control Systems
Operating switches are used in various applications, each tailored to the demands of the system they control:
- Manufacturing and Production: Start/stop functions, emergency stops, and mode selection in production lines and machinery.
- HVAC Systems: Mode control, temperature adjustments, and system power controls in commercial HVAC systems.
- Automotive Industry: Switches for robotic arms, conveyor systems, and safety interlocks in vehicle assembly lines.
- Building Automation: Lighting controls, access systems, and emergency shutdowns in automated building systems.
- Medical and Laboratory Equipment: Start/stop, operational mode selection, and emergency shutdowns in sensitive environments.
Key Benefits of Using Operating Switches in Automation
Operating switches provide numerous benefits across industries:
- Enhanced Control: Switches give operators direct control over machinery, allowing for precise adjustments.
- Safety Assurance: Emergency stops and interlock switches improve system safety by providing immediate shutdown options.
- Versatility: Available in various types, configurations, and mounting options, operating switches can be adapted to different needs.
- User-Friendliness: Simple, intuitive design allows for easy operation, even in complex systems.
Maintenance Tips for Operating Switches
Proper maintenance of operating switches ensures their reliability and longevity:
- Inspect for Wear and Tear: Regularly check switches for damage, such as cracks, loose parts, or corrosion, especially in high-use environments.
- Clean Contact Points: Dust and debris can accumulate on switch contacts, affecting performance. Use contact cleaner or compressed air to remove debris.
- Test Emergency Stops Regularly: Regularly test emergency stops to ensure they function correctly, as these are critical for safety.
- Replace Faulty Switches Promptly: If a switch shows signs of failure, replace it immediately to prevent disruptions.
Troubleshooting Common Issues with Operating Switches
Switch malfunctions can arise from various issues, including mechanical failure, poor electrical connections, or software errors in automated systems.
Loose Connections
Loose wiring can lead to intermittent operation or non-response from switches. Check all connections to ensure wires are secure and terminals are tight.
Mechanical Failure
A switch that doesn’t move smoothly or provide tactile feedback may have an internal fault. For emergency stops, ensure the latching mechanism operates correctly.
Electrical Issues
If switches do not complete circuits, use a multimeter to test for continuity and check for open or short circuits. Faulty switches may require replacement if continuity is absent.
Program or Software Issues
For switches integrated with controllers or PLCs, verify that the control program interprets the input signals correctly. Use diagnostic tools in the programming software to observe real-time input data and troubleshoot logic errors.
FAQs
What is the purpose of an operating switch?
Operating switches control the flow of electricity in a circuit, allowing users to activate, deactivate, or adjust machinery and processes.
How do emergency stop switches work?
Emergency stop switches immediately interrupt electrical current when activated, shutting down equipment to prevent accidents. They remain engaged until manually reset.
What’s the difference between SPST and DPDT configurations?
SPST (Single Pole, Single Throw) switches control one circuit with one on/off position, while DPDT (Double Pole, Double Throw) switches control two circuits with two different positions, allowing for more complex control.
How often should I test operating switches?
Regular testing depends on usage, but emergency stops should be tested frequently, ideally every few months, while standard operating switches should be inspected annually.
What tools do I need for switch maintenance?
Basic tools include a multimeter for electrical tests, wire strippers, screwdrivers, and contact cleaner for cleaning contacts.
When should a switch be replaced?
Replace a switch if it shows signs of wear, intermittent operation, or fails continuity tests, as faulty switches can disrupt operations and compromise safety.
Conclusion
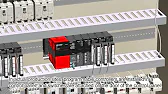
Operating switches are essential elements in control systems, providing direct, user-friendly interaction with automated processes and machinery. By selecting the right type of switch, ensuring proper installation, and following regular maintenance protocols, you can optimize system efficiency, enhance safety, and reduce downtime. In industrial automation, where reliable performance is a must, operating switches provide the control and flexibility required for seamless, efficient operations.