CC-Link IE Field Network – System Configuration for Digital I/O
Setting up the CC-Link IE Field Network for digital I/O allows you to connect and manage various digital devices, such as sensors, switches, and actuators, on a high-speed, reliable network. This guide explains how to configure your system to ensure accurate communication between digital I/O modules and the PLC, with steps covering module configuration, network setup, and addressing.

-
Digital I/O 01 System configuration
CC-Link IE Field Network – System Configuration for Digital I/O Setting up the CC-Link IE Field Network for digital I/O…
-
Digital I/O 02 Hardware settings
CC-Link IE Field Network Connection Guide – Digital I/O Hardware Settings Setting up the hardware for CC-Link IE Field Network…
-
Digital I/O 03 Software settings
CC-Link IE Field Network Connection Guide – Digital I/O Software Settings After configuring the hardware, setting up the software parameters…
-
Digital I/O 04 Operation check
CC-Link IE Field Network Connection Guide – Digital I/O Operation Check Conducting a comprehensive operation check verifies that digital I/O…
1. System Overview and Digital I/O Network Requirements
To establish an effective CC-Link IE Field Network with digital I/O, ensure you have the necessary hardware and software.
Essential Components:
- CC-Link IE Network Module: Connects to the PLC and enables communication with digital I/O modules.
- Digital I/O Modules: Devices that handle digital inputs (e.g., on/off sensors) and outputs (e.g., relays, actuators).
- PLC Unit: Controls the digital I/O devices based on program logic and network communication.
- Network Cables and Connectors: High-quality Ethernet cables for stable, high-speed connections between devices.
Software Requirements:
- Programming Software: Mitsubishi PLC programming software such as GX Works3 for configuration.
- Network Configuration Tool: Often built into the programming software for setting up CC-Link IE Field Network parameters.
2. Setting Up the Network Topology
Design the network topology based on your system’s layout. CC-Link IE Field Network supports a variety of topologies, including star, line, and ring.
Choosing the Topology:
- Line Topology: Best for linear setups where devices are connected in a chain.
- Star Topology: Ideal for systems with centralized control, as each device connects to a central hub.
- Ring Topology: Provides redundancy by looping connections back to the PLC, which can prevent communication loss if a cable fails.
3. Configuring the PLC and Network Module
With the network topology determined, configure the PLC and CC-Link IE Network Module to manage data from digital I/O modules effectively.
Steps for Configuration:
- Install Network Module: Attach the CC-Link IE Network Module to the PLC and connect it to the network using Ethernet cables.
- Assign IP Addresses: Each device on the network needs a unique IP address. Set IP addresses using the network configuration tool to avoid conflicts.
- Set Communication Parameters: In the configuration software, open the CC-Link IE Field Network settings and set communication parameters, including baud rate, data size, and refresh rate.
4. Adding Digital I/O Modules to the Network
Digital I/O modules must be added to the network configuration, allowing the PLC to recognize and manage each module.
Adding and Configuring Digital I/O Modules:
- Open Network Configuration Tool: In GX Works3 or another compatible tool, navigate to the CC-Link IE Field Network section.
- Add Digital I/O Devices: Select each digital I/O module by its model and add it to the network. Assign a station number to identify each module.
- Configure Module Settings: For each module, configure parameters such as input/output modes (sink/source), input delay times, and output response times as required.
- Define Device Addresses: Assign unique addresses to each digital I/O channel. These addresses will be referenced in the PLC program for control and monitoring.
5. Mapping Digital Inputs and Outputs in the PLC
Mapping digital I/O addresses to the PLC ensures accurate control over each device.
Steps of Mapping :
- Access I/O Mapping Settings: In GX Works3, go to the I/O mapping section and link each digital I/O channel’s network address to a device address within the PLC.
- Define I/O Types: Set channels as either digital inputs or digital outputs based on the connected devices.
- Assign Descriptive Labels: Label each input/output with its function, such as “Start Button” or “Relay Output,” to simplify programming and troubleshooting.
- Verify Connections: Once mapped, check each address to confirm it aligns with the physical device locations.
6. Testing the Digital I/O Configuration
After configuring the system, test the setup to ensure all digital I/O modules communicate correctly with the PLC.
Testing Procedure:
- Activate Network Communication: In the PLC software, enable network communication to begin sending and receiving data from digital I/O modules.
- Test Each Input and Output: Manually activate inputs (e.g., press a button) and observe the response on the corresponding PLC input address. For outputs, send test signals from the PLC and observe the activation of connected devices.
- Monitor Status Indicators: Check the status LEDs on each module for signs of connectivity issues, such as flashing error lights, and resolve any detected issues.
- Simulate Operational Scenarios: Test scenarios that reflect normal operation, such as machine start/stop, to validate that the system functions correctly under real-world conditions.
7. Troubleshooting Common Issues
When setting up CC-Link IE Field Network for digital I/O, connectivity issues or incorrect settings may arise. Here are some common troubleshooting tips:
Troubleshooting Tips:
- Address Conflicts: If devices don’t communicate, check for duplicate IP addresses or station numbers in the network configuration.
- Incorrect I/O Mapping: If digital signals don’t register as expected, verify that I/O addresses in the PLC match the device addresses in the configuration tool.
- Network Stability: For intermittent communication issues, inspect network cables for damage or use diagnostic tools to detect any interference.
- Module Status LEDs: Refer to the module’s manual for LED status codes to understand specific error types, such as communication errors or module malfunctions.
Conclusion
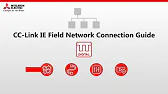
Completing the system configuration for CC-Link IE Field Network with digital I/O allows your Mitsubishi system to effectively manage and monitor digital inputs and outputs across a robust industrial network. By carefully setting up network topology, configuring modules, and testing connections, you can ensure reliable, high-speed communication for controlling connected devices. This configuration is crucial for achieving seamless integration and efficient performance in your industrial applications.