Maintaining a consistent, precise temperature is essential in industries where environmental conditions impact product quality, safety, and energy efficiency. Conducting an operation check on temperature control systems regularly ensures these systems continue to perform effectively. By performing thorough checks, operators can identify early signs of wear, misconfiguration, or malfunction, preventing costly disruptions and maintaining optimal conditions.
This guide provides a detailed look at the temperature control operation check process, from routine inspections to advanced diagnostics.
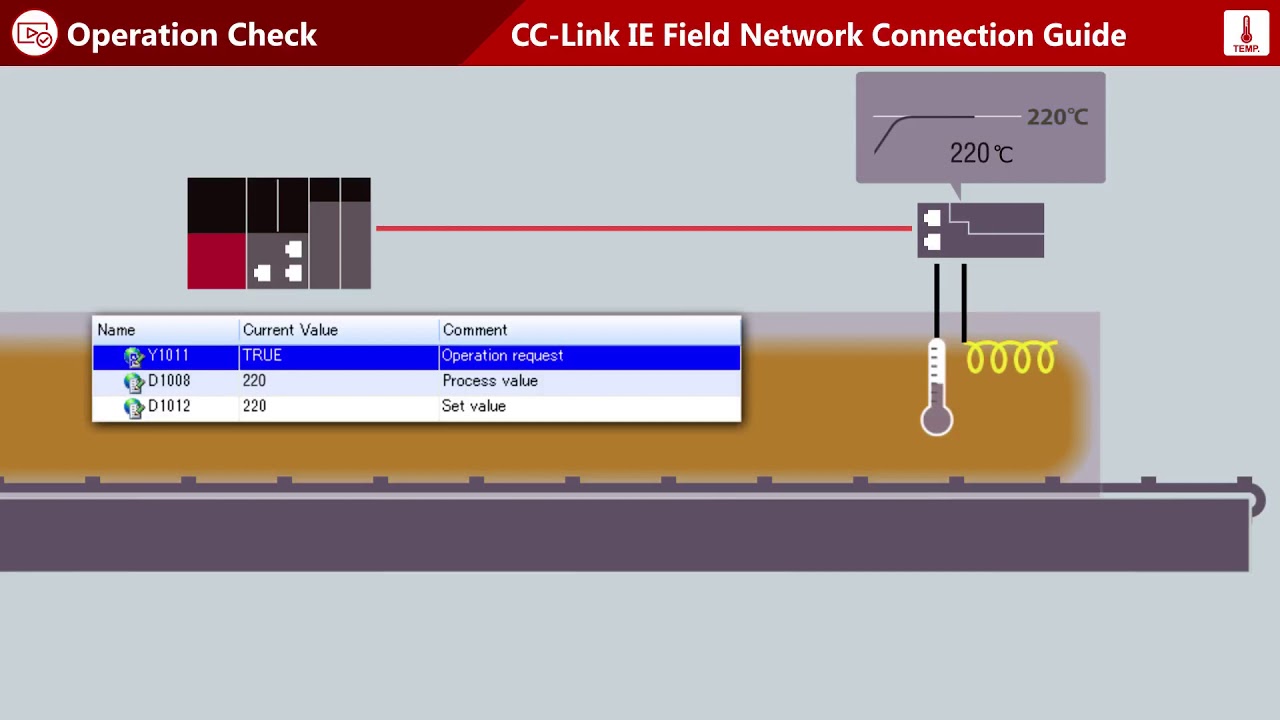
-
01 Temperature Control – System configuration
Temperature control systems play a crucial role in maintaining stable environmental conditions in various industries. By ensuring optimal performance, these…
-
02 Temperature Control – Hardware settings
Temperature control systems rely heavily on precise hardware settings to achieve the stability required for consistent and efficient performance. From…
-
03 Temperature Control – Software settings
Temperature control systems not only rely on hardware but also incorporate sophisticated software settings to streamline operation, increase accuracy, and…
-
04 Temperature Control – Start up
Starting up a temperature control system for the first time or after maintenance requires careful attention to ensure smooth and…
-
05 Temperature Control – Operation check
Maintaining a consistent, precise temperature is essential in industries where environmental conditions impact product quality, safety, and energy efficiency. Conducting…
The Importance of Regular Temperature Control Operation Checks
Regular operation checks verify that the temperature control system is functioning as intended. These checks help prevent system downtime, reduce energy waste, and enhance safety by detecting issues early. Moreover, they provide the assurance that temperature-sensitive processes remain within defined limits, protecting both equipment and product quality.
Key Components to Check in Temperature Control Operation
Controllers
The controller is the system’s central unit, responsible for receiving data from sensors and sending commands to actuators. Checking the controller includes:
- Parameter Verification: Ensure control parameters, such as PID (Proportional-Integral-Derivative) settings, are aligned with current operational requirements.
- Response Test: Adjust setpoints temporarily to observe how quickly and accurately the controller responds.
- Firmware Updates: If applicable, ensure the controller’s firmware is up-to-date for security and performance.
Sensors
Accurate temperature detection is crucial for stable control. During operation checks, examine sensors for:
- Calibration Consistency: Verify that sensors are calibrated and providing accurate readings.
- Physical Condition: Look for any physical damage, such as wear on sensor housing or wiring.
- Data Stability: Confirm that sensors provide stable, consistent data with minimal fluctuations under constant conditions.
Actuators
Actuators like fans, heaters, and coolers execute the controller’s commands to regulate temperature. Check actuators by:
- Response Time Testing: Ensure actuators engage and disengage quickly in response to controller commands.
- Inspecting Wear and Tear: Look for any signs of mechanical wear that could impact performance.
- Noise and Vibration Checks: Abnormal noises or vibrations may indicate impending failures or alignment issues.
Power Supply and Wiring
A stable power supply is essential for reliable temperature control. Inspect power supply and wiring by:
- Voltage and Current Testing: Verify the system receives stable voltage and current within specified ranges.
- Inspecting Cable Integrity: Check wiring for wear, insulation damage, and secure connections.
- Grounding Confirmation: Ensure that all components are properly grounded to reduce electrical risk.
Operational Parameter Checks
Temperature Setpoint and Range Verification
Verify that the setpoints and ranges align with operational needs. Any deviation from the intended temperature range can compromise system performance:
- Setpoint Accuracy: Compare setpoints with actual operating temperatures to confirm accuracy.
- Secondary Range Settings: For systems with multiple modes, check that secondary temperature ranges are correctly configured for each mode.
- Alarm Thresholds: Verify that alarm settings reflect operational safety limits, activating when temperatures exceed safe boundaries.
Control Mode Review
Check the control mode, especially in applications that demand high precision. For example, PID control may require tuning if conditions or requirements have changed:
- Proportional, Integral, and Derivative (PID) Settings: Fine-tune PID parameters to enhance responsiveness and prevent overshooting.
- Adaptive Control: For systems with adaptive modes, confirm that the system adjusts automatically to variations.
- On-Off Control Verification: In simpler setups, confirm that the on-off mechanism toggles correctly without causing fluctuations.
System Diagnostics and Testing
Running Diagnostic Software
Many temperature control systems include built-in diagnostic tools or support external software diagnostics. Run diagnostics to:
- Detect Hidden Faults: Diagnostics can reveal issues like data inconsistencies or latent faults that aren’t visible during routine checks.
- Analyze Historical Data: Review past performance data to identify patterns or trends that might indicate degradation.
- System Health Reports: Generate and review reports on system health, error logs, and alarm history.
Conducting Manual Function Tests
Manual testing provides insight into the system’s real-world performance. Tests to consider include:
- Alarm Test: Manually trigger alarms to ensure that all notification settings function as intended, including visual and audio alerts.
- Cycle Tests: Run through several heating or cooling cycles to verify that actuators respond appropriately and maintain temperature stability.
- Failsafe Function Test: Simulate conditions that trigger failsafe mechanisms, such as power interruptions, to ensure the system handles emergencies correctly.
Monitoring and Analyzing Operational Data
Reviewing Data Logs
Data logs offer valuable insights into system performance and can help detect trends over time. For effective data log analysis:
- Temperature Fluctuation Tracking: Examine logs for recurring fluctuations that might signal an issue with control settings or hardware.
- Energy Consumption Trends: Analyze power usage to spot inefficiencies, helping identify potential energy-saving adjustments.
- Alarm and Alert Analysis: Review past alarms to identify patterns that may indicate specific issues, such as overheating at particular times or during certain cycles.
Trend Analysis for Proactive Maintenance
Predictive maintenance relies on trend analysis to identify components that may need attention before they fail. Use trend data to:
- Identify Calibration Drift: Look for gradual changes in sensor readings that may indicate a need for recalibration.
- Actuator Wear Detection: Track performance declines in actuators, such as slower response times or increased cycle frequency.
- Performance Optimization: Make proactive adjustments based on trends, optimizing the control system’s overall stability and efficiency.
Responding to Operation Check Findings
Performing Adjustments and Calibration
If checks reveal inconsistencies or inaccuracies, recalibrate components or adjust parameters:
- Sensor Recalibration: If sensors show drift or inaccuracies, recalibrate to ensure precise readings.
- Actuator Realignment: Adjust actuators that show signs of wear or misalignment, ensuring smooth operation.
- Parameter Fine-Tuning: Fine-tune control settings, such as PID parameters, for better stability and accuracy.
Documenting and Scheduling Follow-Up Checks
Record all findings, adjustments, and recommendations for follow-up checks. Documentation is essential for:
- Tracking Historical Performance: Maintaining records helps assess long-term performance and informs future adjustments.
- Planning Maintenance: Use findings to schedule regular maintenance tasks, like calibration and cleaning, based on identified needs.
- Continuous Improvement: Reviewing documentation over time helps improve operational checks, refining procedures and increasing efficiency.
FAQs
What is an operation check in temperature control systems?
An operation check verifies that all system components, such as controllers, sensors, and actuators, are functioning as expected and that the system meets temperature control requirements.
How often should I perform an operation check on a temperature control system?
The frequency depends on the application, but a monthly or quarterly check is common. High-stakes applications may require more frequent checks.
What are some signs that a temperature control system needs maintenance?
Signs include temperature fluctuations, alarms triggering frequently, increased energy consumption, and delayed actuator response times.
What are the key steps in an operation check?
Key steps include verifying controllers, sensors, and actuators; checking power supply and wiring; running diagnostics; and analyzing operational data.
How can data logs help in operation checks?
Data logs provide insights into temperature trends, power usage, and alarm frequency, helping detect patterns that may indicate the need for adjustments or repairs.
Why is it important to verify temperature setpoints during an operation check?
Verifying setpoints ensures the system maintains the desired temperature range, preventing potential damage to sensitive materials or equipment.
Conclusion
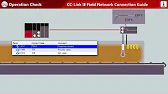
Performing a comprehensive temperature control operation check is vital for maintaining consistent performance and safety. By systematically inspecting components, verifying parameters, running diagnostics, and analyzing data trends, you can ensure that the system operates reliably. Regular operation checks not only extend the life of temperature control equipment but also safeguard product quality and energy efficiency, making them an essential part of system maintenance.